Bottling Plant
Facility Improvements
CLIENT
Beverage Producer
PROJECT SCOPE
Facility Improvements, Bottling-Packaging-Palletizing Line Installation:
Civil, Structural, Mechanical, Electrical
INDUSTRY
Manufacturing, Food & Beverage
LOCATION
Western United States
Site Renovations Expand Capacity for New Production System
Installation Completed without Downtime for Existing Operations
SilMan was engaged by a leading engineering firm to support a national beverage producer at their bottling plant in Northern California. This multi-phase project repurposed 3k sqft of production space to accommodate the bottling line and packaging system.
The primary challenge for the SilMan Team was to seamlessly provide the infrastructure, mechanical, electrical, and intra-logistics for the new system without interrupting ongoing operations. Including demolition.
The undertaking required the coordinated deployment of SilMan’s Civil, Structural, Mechanical, and Electrical teams.
This “from the ground up and walls in” project is a perfect showcase of the efficiency and cost-savings provided by SilMan’s self-performance.
“Under One Roof” – as it is known by team members – is a strategic management approach that directs a broad range of in-house skilled teams and minimizes third-party contractors. This capability allows SilMan to deliver unique value to clients beyond simply “on time and under budget.”
Beverage Producer Capitalizes on Growth
In an effort to continue their expanding market share, the beverage maker sought to expand the capacity of their existing, without new construction.
Specifically, the new production line provides a bottling operation for 96oz cartons for multiple products, dairy and non-dairy.
Coordination of Trades
Project Management Methods Deliver Successful Outcome for Client
SilMan’s “one-stop-shop” structure allowed our teams to continuously coordinate with stakeholders throughout the entire project. Powered by a single management team and SilMan’s cloud-based project management platform.
This proven approach provides a smooth hand-off from phase to phase and between trades, with updates on a daily – even hour to hour – basis.
Since our trade teams share a single management resource, tangible benefits accrue to our clients:
- Reduced Change Orders resulting from inefficiencies and out-of-sync contractors.
- Increased efficiency from streamlined communication with a point of contact for all trades.
- Maintain the schedule by mitigating slowdowns and bottlenecks from multiple contractors.
In the end, however, there is only one real measurement of success: being invited back!
In this case, the value of the SilMan approach is borne out by the fact that both the Construction Manager and end-user continue to engage SilMan on a nearly continuous basis:
- Maintenance and repair of equipment
- Installation of updating of equipment and controls
- Updates to facilities and infrastructure
In essence, SilMan has become an extension of the client’s in-house resources.
SilMan provides a cost-effective pool of highly skilled trades to keep their people, plant, and equipment operating at maximum productivity.
As Jeff Piazza, leader of the Site Services teams, says “we’re the easy button. One call and the whole thing is handled.”
Enough said! Let’s take a closer look at the scope of work.
Speak to a key team member on this project
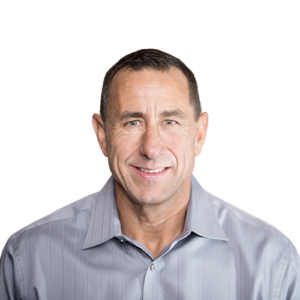
Meet Jeff Piazza
For more information about this project or related topics, contact Jeff by email or call directly at 925.984.0062
You may also enjoy this article
Gallery: Site Improvements in Progress
A new 96oz bottling system is the central focus of a newly transformed space in beverage plant.
Civil and Structural Infrastructure
New drainage, flooring, and overhead support
As the first to arrive, the SilMan Civil team provided the foundation for the project…literally.
The client’s object was to convert an area within their existing plant for new uses. To accomplish this, our team needed to establish electrical and water utilities, and a foundation that would support the introduction of industrial beverage lines, automated packaging systems, and shipping equipment – from below and above.
Additionally, all drainage for process equipment and floor drains were tied into the existing drainage system to properly move wastewater to the client’s internal water treatment plant, before being released to public utilities.
Before commencement of work, a temporary dust barrier was erected to protect the ongoing bottling area operations in the facility.
Below Ground and Flooring
- Trenching
- Excavation and grading
- Process drains
- Moisture barrier
- Concrete
With the infrastructure in place, SilMan engineered and fabricated an access platform and operator platform for the new operation, including stairway and handrailing. Additional structural support was provided for new overhead pipe and conveyor lines to be installed.
The team poured 87 yards or 2900 sq. ft. of concrete, with depths up to 10 inches.
Finally, the team provided a number of finished work items:
- Epoxy coated flooring
- Hand and eyewash stations
- Floor drains
- HMI Stands
- Bollards
- Fabrication of pipe support racks
- Argelith porcelain tiles
The duration of the civil and structural phase was four months.
Installation of 96 oz. Packaging Line
SilMan Millwrights provided installation services for all bottling, material handling, and utility equipment.
Installation of all components includes OEM provided brackets and mounting, fabrication and installation of mounting brackets, anchors or beams, and installation of compressed-air lines.
Modification of guide rails was also required for several locations.
Process and Material Handling Equipment
- Proprietary Bottling Equipment
- Intelligrated Conveyor and Sortation
System and Process Equipment
- Dyco Semi-Auto Debagger, with side grip elevator and side grip lowerator.
- Installation of single file bottle conveyor from lowerator to infeed
- Air Scrubber Skid
- UV Water Treatment Skid
- Domino Coder.
- TapTone Compression Inspection
- Polyketting FIFO Buffer Table
- Arol Capper
- System Cap Inspection System
- JetAir Tunnel
- E.Rotary Labeler
- KHS Case Packer
- Diagraph Case Printer
- FT System Checkweigh Inspection system
- Ambaflex Case Spiral
- Intelligrated Palletizer
Innovation and Collaboration
SilMan’s culture and wide range of skilled in-house teams have allowed the company to flourish as a partner for organizations seeking to create piot projects. We have supported a new initiative intended for repeated iterations for Siemens Logistics (Visicon singulator technology), Bay Area Rapid Transit (BART subway canopies), and multiple national programs for leading parcel and fulfillment companies (conveyor line modifications). These collaborative opportunities allow project owners to assess the scope of work, processes, time, and budget needed for each repetition.
Learn more about SilMan’s in-house skilled trades and project resources.
Power and Electrical Systems
The electrical installation scope of work includes all of the above-listed equipment.
Installation of electrical infrastructure was also provided: conduit, power, ground and support structure, and network wiring and communication for motors, network, e-Stop, sensors, stack lights, horns, and local control stations.
- Motor Primary Power
- Accumulation Table Infeed Motor Install (TS-A700)
- Case Conveyor E24 Motor Power Supplies
- Case Conveyor IO Power Supplies
- Control Wiring
- Ethernet Communication Wiring
- Fiber Communication Wiring
- Work Order Computer Wiring
- Emergency Stop Wiring (Machine Centers)
- Interlock Wiring to OEM Equipment
- P12 Main Conveyor HMI Installation
- P12 Pallet Conveyor HMI Installation (HMI-B650)
- Dyco Debagger
- Dyco Cable Conveyor
- Procurement and Installation of 4”x4” wire from the elevator control panel to lowerator control panel.
- Installation of conduit and wire for devices and motors
- Procurement and installation of cable sensors. Sensors will be pre-mounted by OEM.
- Filler Network Wiring
- Polyketting Accumulation Tables(6)
- AROL Capper
- PE Labeler
- KHS Packer
- Alvey Palletizer
- TapTone Pressure Inspector and Rejector
- FT Cap Inspector and Rejector
- FT Case Inspector and Rejector
- JetAir Bottle Dryer
- UV Acid Skid
- Acid Scrubber Skid
The duration for all mechanical and electrical services was six months.
About the Company
SilMan Industries (previously SilMan Construction) is based in San Leandro, Calif., with Engineering and Field Operations offices in Tupelo, Miss. The firm provides integrated turnkey solutions in the Industrial, Manufacturing, Distribution, and Public Works sectors.
Notably, in 2010 SilMan Industries was contracted to dismantle and remove the NUMMI assembly line in Fremont, Calif., transport the equipment, and reinstall the system in Blue Spring, Miss., establishing Toyota Motor Manufacturing Mississippi (TMMMS). This high-visibility project ignited the company’s meteoric growth, laying the foundation for SilMan’s national service area.
For more information, please visit www.silmanindustries.com/about.