Aviation Operations:
Air Cargo Handling
ULD Ground Support System


CLIENTS
United Parcel Service
Port of Oakland
INDUSTRY
Airport Operations
Air Cargo Terminal
Public Works
PROJECT SCOPE
Civil, Mechanical & Electrical Installation, Power, Controls
Summary: Air Terminal Ground Operations
This article surveys an air cargo handling equipment implementation, deploying civil, mechanical, and electrical teams to provide caster decking, scissor lifts, scales, electrical controls, and electrical infrastructure in support of the ground operations at the transfer terminal for a leading parcel carrier at the Port of Oakland. The new air cargo handling equipment and accompanying infrastructure provide improved connectivity between air, land, and warehouse operations.
Air Cargo Handling Systems
Ground Support Operation is Key to Competitiveness
The parcel and logistics industries have faced unprecedented growth in volume, a trend that was already in place before the pandemic of 2020. Moreover, stiffening competition means there is no end in sight for the continued improvements of speed and efficiency at every stage of transport, sortation, and delivery that are in development.
This article explores Phase 2 of an ongoing three-phase project at the UPS air cargo handling terminal in Oakland, in partnership with the Port of Oakland.
Phase 1 of this project required the installation of 47k sq/ft of caster deck. You may learn more about that project, including photos, here.
Air Cargo Handling Equipment
Caster Deck and Scissor Lift Support
Leading parcel carriers like the one featured in this case study are adding value to their air freight transfer terminals through the deployment of caster decks and lifts. This project allows the carrier to presort and efficiently direct cross-dock, intermodal, and through-traffic as the ULDs are offloaded from aircraft.
These improvements to their air cargo handling equipment and systems allow the carrier to expand capacity and improve efficiency.
Moreover, the design provides ergonomic advances to provide a safer work environment for team members working with ULD transfer and sortation.
Speak to a key team member on this project
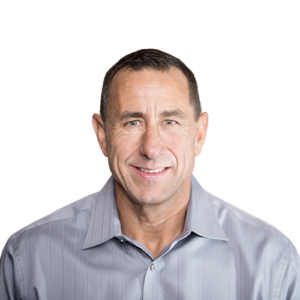
Meet Jeff Piazza.
For more information about this project or related topics, contact Jeff by email or call directly at 925.984.0062.
You may also enjoy this article
Phase Two: Air Terminal Facility Update
Electrical and Mechanical Implementation of Air Cargo Handling System
The project, properly known as “Caster Deck, Scissor Lift and Scale Installation, Phase 2” directs the installation of equipment and electrical infrastructure to power 22 lifts and 5 scales that will seamlessly operate within a large-scale caster deck system, some of which has been previously installed.
Four distinct areas of work were employed for this undertaking:
- Electrical Infrastructure (conduit, wiring, panels, breakers)
- Civil
- Mechanical (Equipment Installation)
- Control Power (power supply to support lifts and scales)
Electrical: Primary Power
The Primary power requirements for the system necessitated extensive underground wiring, conduit, and grounding. See “Civil Construction” below.
Panels installed include 400-amp (1) and 100-amp (2), 30kva transformer and 120v panel, and 22 Lithonia lighting fixtures with motion sensors.
The project also adds 7 light poles to the area.

Civil Construction: Concrete and Trenching
Installation of primary power to the tarmac-based air cargo handling equipment required considerable civil construction in order to support underground wiring (power supply) and footings for equipment and supports.
Highlights
- 44 Wide flange columns, 10’ tall, for 22 lifts, 2’ x 4’ or 2’ x 6’ depending on single or double I-beam placement
- 3’ x 4’ x 200’ primary power run
- Saw cut, demo, and off-haul of 15’x311’ area of existing 12” AC.
- 15’ x 310’ 4000psi concrete pad, 12” depth
- #4 rebar cages and ties at each I-beam footing location.

Equipment Installation
The SilMan Millwright team provided mechanical support to implement the air cargo handling equipment, including 22 Scissor Lift Tables (10 new, 12 repurposed).
The installation of 5 ULD (Unit Load Device) weigh scales, however, was a particular challenge. Each of the five scales was inserted into the existing caster deck section, requiring the removal of caster deck panels, and fastening of the ULD scales into the newly created space.

Electrical: Control Power
The new air cargo handling systems presented a number of challenges to the electrical team, in particular the scale of the project.
The installation of raceway and conductors to 22 lifts and 5 scales required managing a work area that spanned nearly 50,000 sq./ft.
Moreover, the electrical team faced the challenge of wiring this enormous space for scales and control panels in a vertically limited crawl space beneath the deck, measuring 12-14” inches deep. This circumstance required the electrical team to spend several weeks crawling and laying on their back as they perform their handiwork.
Breaker installation necessitated extensive (months of up-front) coordination with the Port of Oakland, requiring the shutdown of significant portions of the airport, including the air cargo and commercial terminals, and three airlines.

In this photo, millwright Shane Benson is shown extending his arm while lying on the tarmac to offer a sense of the cramped conditions.
Photo Gallery
Photo Credits: SilMan Industries Site Services team members.
Ground Support System Implementation
Meet Key Team Members
Engineering Partners
The engineering component of this project was especially critical to the successful implementation of the project, and the final satisfaction of the client. In this light, the contribution of Brandon Yee (Electrical, YEI Engineering) and David Brown (Civil, Adobe Associates) cannot be overstated.
The team was tasked with the design and engineering to add 22 scissor lifts and 5 scales to an existing caster deck. To make this directive a reality, we turned to two partners in the SilMan community who were familiar with the processes at the Port of Oakland. Mr. Yee engineered our e-GSE charging stations project in 2018, and Mr. Brown is a long-time associate with whom we have joined forces on numerous projects at the Port and beyond.
The leadership team of Brandon, David, and Chris worked many a late night to develop a design that would satisfy the rigorous safety and environmental standards of the client.
In the end, engineering and the permitting process required a full year to complete, clearing our execution team to begin work onsite in January 2020, immediately following the peak parcel delivery season.
Lastly, Jeff Piazza, who provides senior leadership for the Site Services division at SilMan, also played a crucial role in cost estimation and providing sage advice and direction.
Meet the SilMan Site Execution Team
Air Cargo Handling Terminal Project Put Multi-skilled In-House Talent in the Spotlight
We are grateful for the collaborative atmosphere and pride that our teams bring to their work. Here are the exceptional tradesmen that made this undertaking a success.
Scott Cully – General Foreman
Shane Benson – Millwright
Hugo Padilla – Electrical Foreman
Armando Ramirez – Electrical Apprentice
Justin Neely – Electrical Management
Rafael Cornejo – Civil Management
Jose Martinez – Civil Lead
Maria Salazar – Project Coordination
Mike Watchers – Safety Management
On a Personal Note
Lastly, when we approached for final comments on the project, Chris Fredrickson had this to say in the wake of the successful completion of this venture:
“Based on the critical nature of this installation, we chose our team with great care. We brought in Scott Cully who had recently completed our CityLift project in Olympia and I can’t say enough about this gentleman’s skill and attention to detail. We also brought in Shane Benson who is an exceptionally talented young millwright, who takes initiative to get the job done.
On the electrical side, we brought in newcomer Hugo Padilla, who worked for us as an apprentice on the Oakland Airport baggage system CBIS project (2018) and continues to show tremendous promise. We were also pleased to have another young talent, Armando Ramirez, as an apprentice. Under the guidance of Justin Neely, these guys killed it!
None of this would have been possible without our civil team, who literally “paved” the way for all the infrastructure necessary to make this project a success. Thank you, Rafael Cornejo and Jose “Mini” Martinez and your team of miracle-men who made small potatoes out of a very large, tough job.”
About the Company
SilMan Industries (previously SilMan Construction) is based in San Leandro, Calif., with Engineering and Field Operations offices in Tupelo, Miss. The firm provides integrated turnkey solutions in the Industrial, Manufacturing, Distribution, and Public Works sectors.
Notably, in 2010 SilMan Industries was contracted to dismantle and remove the NUMMI assembly line in Fremont, Calif., transport the equipment, and reinstall the system in Blue Spring, Miss., establishing Toyota Motor Manufacturing Mississippi (TMMMS). This high-visibility project ignited the company’s meteoric growth, laying the foundation for SilMan’s national service area.
For more information, please visit www.silmanindustries.com/about.