Industrial Furnace
Foundation and Structure
CLIENT
Glass Bottle Manufacturer
PROJECT SCOPE
Building Foundation
Steel Erection
INDUSTRY
Manufacturing, Beverage
LOCATION
Western United States
Industrial Furnace Project Overview
SilMan Industries was engaged by a leading bottle producer to provide the concrete foundation and steel structure for a new industrial furnace, one of five at the facility.
The remaining four furnaces were fully operational throughout the course of construction, creating a high-heat work environment and complicated logistical situation.
Furthermore, since the furnace structure to be replaced was situated between two operational furnaces, delivery of materials and large equipment to the work area was achieved by a hydraulic crane through the roof of the facility.
The project was completed on schedule by precise planning of internal teams, cooperation with subcontractors, and collaboration with the client.
[NOTE: CLICK ALL PHOTOGRAPHS FOR FULL-SCREEN VIEWING]
Building Foundation and Structural Steel
Glass Manufacturing Support
The furnace project was a multiphase undertaking with two main areas of work:
- Provide a concrete foundation to support the new furnace
- Erect an 80 ft. tall, five-floor steel structure-within-a-structure with production space on each level
- Additional performance: Steels stair cases were fabricated on site and installed, replace stack, remove and replace roofing & siding to allow overhead access to the job site
Speak to a key team member on this project
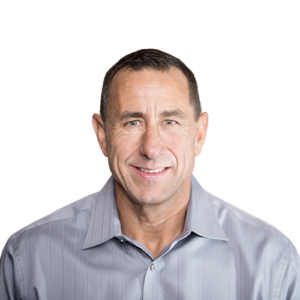
Meet Jeff Piazza
For more information about this project or related topics, contact Jeff by email or call directly at 925.984.0062
You may also enjoy this article
Project Highlights “At-a-Glance”
Building Foundation
2,000 cubic ft. of concrete |
---|
Mat slab, double-plate rebar, grade beams |
Concrete pad to support furnace |
Footers, base plates for 80’ tall steel structure |
Fly in earth moving equipment by crane |
Steel Erection
1,250 tons of steel |
Steel erection bolted and welded |
Fly in all large tooling, equipment and bolted frames by crane |
Replace roofing and siding |
Fabricate stairs onsite, crane in, and install |
Install stack |
Portions of the roof and siding were removed in order to provide access for materials and equipment to be transferred into the work area. Roofing and siding were replaced with virgin material at the conclusion of the project.
Site & Project Management
In addition to concrete and steel, project management for the newly constructed furnace included coordination of multiple concurrent trades, as well as safety and site management.
Trades utilized include Millwright, Iron Worker, and Civil Teams.
The project required 12 months to complete.
Continue reading to learn more about the unique challenges encountered during this project.
Gallery: Civil Construction & Foundation
Scope of work: Concrete Slab, Double-Plate Rebar, Base Plates, Footers
Industrial Project Management
Challenges and Achievements
The furnace infrastructure implementation was completed without interrupting ongoing glass bottle production. The successful outcome was achieved by the planning and scheduling expertise of the SilMan project managers and daily coordination with the client.
As always is the case, communication is king!
This key result, however, was also the key challenge.
Throughout the project, our trade professionals were implanted deep within a fully operational glass production facility. Four furnaces operating 24 hours a day.
This environment required two specific areas of focus for project managers:
- The manner in which materials and equipment could be moved into and around the job site
- How to accommodate the volume of team members, equipment, and tooling that would be present in limited workspaces
In the end, high levels of flexibility and collaboration proved to be the crucial elements that allowed our trade teams to work safely and productively.
Gallery: Steel Erection
Girders and Beams – Stairways – Stack
Crane Rigging
Challenge: Access to Work Area
Transporting materials and equipment to the job site was a daily challenge.
The location of Furnace 2 necessitated that all equipment and material be craned into the work area over Furnace 1. A portion of the Furnace 2 roof was removed in order to fly and land items into the work area.
In addition to transporting raw materials into the facility, preassembled frames were also flown in. Steel stairwells were also fabricated on site and placed by crane.
Continuous rigging and hoisting required constant attention by the safety team:
- Large equipment, steel members, and preassembled steel frames passed over the adjacent structure
- Crane lands equipment and materials through an opening of the worksite roof
- Traffic control management around staging and crane operations
Industrial Project Management
Challenge: Dynamic Environment
The working conditions themselves required constant vigilance.
Moreover, working in close quarters with multiple concurrent trades required constant attention to schedules, and location of tooling and supplies in order to maintain productivity, avoid trip hazards, and provide clear egress.
Furthermore, team members worked in close proximity to the neighboring furnaces. At times, SilMan’s trade professionals could be an arm’s length from gas and air lines, electrical panels, and fully operational machinery.
Lastly, the summer sun was compounded by the heat created by furnaces on each side of the work area. This presented a constant threat of heat illness and related risks.
Gallery: Iron Workers Near Operational Furnace Equipment
Innovation and Collaboration
SilMan’s commitment to self-performance and communication provides efficiency and cost optimization for clients.
Learn more about our In-House Skilled Trades & Project Resources.
Construction Site Safety Management
Industrial Safety Best Practices
Given the scale and risk factors of the project, Safety was the most serious aspect of this project.
SilMan’s safety team provided an extensive JHA and a safety manager on-site at all times. Common best practices were followed, including daily “toolbox talks,” site audits, and clearly posted materials as a resource for common questions, and safety tips.
Heat
During warmer months, stretching from May to September, the risk of heat illness dominated the safety team’s attention.
However, with offices in California and Mississippi, SilMan’s team is well-versed in precautionary habits and identifying the early signs of overheating.
The heat produced by the surrounding active furnaces contributed to heat-related risks, even when the weather cooled.
Overhead Activity and Hazards
Once the foundation was complete and structural work commenced, team members were constantly working on multiple elevations within the facility.
Additionally, continuous rigging and hoisting required constant attention by the safety team:
- Large equipment, beams, and preassembled steel frames passed over power lines and an adjacent structure
- Crane lands equipment and materials through an opening of the worksite roof
This constant activity on multiple floors and in the air underscores the importance of daily safety awareness sessions. In these meetings, fall protection protocols and the safe stowing of tools and materials to avoid falling objects were constant topics.
Pace of Work and Fatigue
The schedule required long hours and a seven-day work week.
Risks that accompany these circumstances include team morale, efficiency, and safety.
Both the heat of the construction site and the strenuous schedule were compounded by the crowded work areas.
Other active trades on the site included bricklayers, pipefitters, and insulation installers. Additionally, the close proximity of operational furnace equipment required constant vigilance.
In order to combat these challenges, team member days-off schedules were closely managed, as well as rest and recovery during the workday.
Gallery: Team SilMan on the Job
Glass Manufacturing
How Are Glass Bottles Made?
The glass bottle manufacturing process begins with “Cullet,” the raw material from which glass is made. The Cullet is heated to a molten state and injected into molds to produce a bottle or other glass implement. The new bottles are cooled before being advanced either to the warehouse for storage or immediate distribution. Each type of bottle has its own unique “recipe” for raw materials, temperature, and treatment.
For large-scale facilities, induction and movement of materials is an automated process. Glass manufacturing machinery and equipment includes elevators for moving cullet trucks and ground storage, and trough conveyor systems that sort and direct raw materials to the proper furnace for processing.
Lastly, highly specialized automated material handling systems move single finished bottles through storage and packaging processes. From there they are either moved directly into bottling operations or palletized for delivery.
Industrial glass bottle manufacturing plants can produce thousands of bottles each day.
The industrial furnace is the most iconic glass-making equipment. Commonly known as the “hot end” of the process, glass bottle manufacturing furnaces reach temperatures in excess of 2,000 degrees Fahrenheit.
The furnaces are the heart of the system, typically made from brick. The useful life of the furnaces is approximately 12 years, due to the effects of high heat on the bricks and insulation.
About the Company
SilMan Industries (previously SilMan Construction) is based in San Leandro, Calif., with Engineering and Field Operations offices in Tupelo, Miss. The firm provides integrated turnkey solutions in the Industrial, Manufacturing, Distribution, and Public Works sectors.
Notably, in 2010 SilMan Industries was contracted to dismantle and remove the NUMMI assembly line in Fremont, Calif., transport the equipment, and reinstall the system in Blue Spring, Miss., establishing Toyota Motor Manufacturing Mississippi (TMMMS). This high-visibility project ignited the company’s meteoric growth, laying the foundation for SilMan’s national service area.
For more information, please visit www.silmanindustries.com/about.