Machinery Rigging and Moving
PROJECT SCOPE
Machinery Rigging and Moving, Commission, Decommission, Equipment Relocation, Project & Site Management, Safety Management
INDUSTRIES SERVED
Manufacturing, Material Handling, Food & Beverage
Installation, Demolition and Relocation
Machinery Rigging and Moving: the Industrial Life-Cycle
We commonly consider machinery rigging and moving as focused on ultra-large equipment, but there is much more to the story.
The pursuit to maximize ROI on industrial equipment reaches far beyond the purchase price, installation, and operating costs. Keeping machinery healthy through regular maintenance and repair is crucial. In the end, the highest use for a piece of equipment, or entire systems, is to be removed to make room for newer, more productive equipment and technology; which must also be conducted in a cost-effective manner.
Riggers stand at the beginning and the end of this life-cycle. In this article, we will offer a brief explainer about their unique contribution, as well as share highlights from a few of our own machinery rigging and moving projects.
We have selected four rigging projects to highlight the breadth of applications that riggers support. Along the way, we will also highlight the depth of preparation and risk assessment undertaken by riggers to safely perform their work.
We will also hear from Rob Hernandez, who leads and coordinates the SilMan Millwright team.
But first, a little background.
What is Machinery Rigging and Moving?
Some of our readers may not have a complete understanding of the rigging specialization. Here is a short primer to get you going!
As you might guess, Riggers garner their trade name from its origins in the maritime profession. The process of lifting objects through the use of hoists and pulleys has been adopted in many other industries beyond sailing ships.
Today, Rigging refers to any lifting, securing or moving of heavy objects. Specifically, rigging in industrial settings refers to the movement of large equipment.
But this definition does not fully describe the skills and day-to-day contribution that these tradesmen provide.
SilMan riggers are highly-trained mechanical specialists, also known as Millwrights. They are equipped to provide end-to-end support of industrial equipment: installation, maintenance, repair, and commission/decommission. And, of course, on each end of that cycle, rigging and relocation.
Given the abilities of the SilMan Millwright team, rigging projects are a showcase for their wide range of abilities.
Here are a handful of memorable machinery rigging and moving projects completed by our Millwright Riggers.
Speak to a key team member on this project
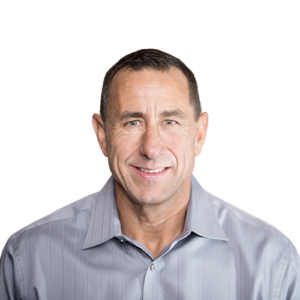
Meet Jeff Piazza
For more information about this project or related topics, contact Jeff by email or call directly at 925.984.0062.
You may also enjoy this article
Best Practices for
Rigging and Moving Equipment:
Project Case Studies
1. Critical Picks
Dairy Machinery Rigging and Moving
When a Northern California dairy producer came to SilMan with two equipment decommission and removal projects, our Millwright team rose to the moment. In each case, the equipment being moved was fully in its productive life, so the equipment needed a gentle touch in order to guarantee continued fruitful use.
One of the projects involved our client’s purchase of equipment from another dairy. The scope of work for this project was massive, including the decommissioning of dozens of machines and hundreds of spare parts.
The SilMan Millwrights, supported by our in-house Electrical team, managed the entire removal: from decommission, rigging, removal, to final load and tie-down on ground transport.
Additional details include the creation of an inventory system, labeling, photolog, and match marks components for re-assembly.
What is a Critical Pick?
A critical pick is a lift that involves two different lifting sources, such as a crane and a hoist, or a load that exceeds 75% of the rated capacity of the crane.
In this case, the silos, reaching up to 40’, are especially challenging due to their size and peculiarly lightweight. In addition to a crane, hoists were used to level these towering cylinders. Spreader beams were also employed to load onto flatbeds. These are the rigger’s primary tools for such pieces.
38 pieces of equipment were removed and rigged for ground transportation. In addition, dozens of fabricated boxes and loaded pallets were prepared to accommodate related equipment and components.
The project required four weeks to complete and 40 trucks to transport the equipment to their new home.
This collection of images captures the lifts from this project as well as scenes from an additional beverage client in which six silos were relocated.
2. Pipe Mill Demolition and Relocation
Machinery Demolition and Rigging for Factory Shutdown
This project required the decommissioning and removal of an entire pipe mill operation.
The scope of work covered material, equipment, and site services for the dismantling, removal, packaging, preparation, and loading of all mechanical equipment, electrical equipment, nominated overhead cranes, and spare equipment. SilMan also managed ground transportation to a lay-down site provided by the customer.
The sheer volume of pieces, including mechanical and electrical components, required highly detailed planning for movement and staging to keep the area productive and safe.
In particular, low overhead clearance and narrow traffic areas were specific challenges for the SilMan riggers.
SilMan’s Safety Team provided a JHA prior to the team arriving on site. Nonetheless, a safety manager was present daily to assist site leadership in the implementation of a Safe-Lift Plan for each piece and to participate in team coordination meetings.
The project took four months to complete.
Hazardous and Non-Hazardous Waste
In addition to the mechanical and electrical tasks, SilMan was also responsible to drain and dispose of all industrial substances from the site.
And if you know anything about California, you know something about the scale and detail of this undertaking.
Non-hazardous waste can be recycled, but hazardous waste must be removed and disposed of according to the regulation for each substance.
The waste management scope of activity included facilitating and compiling test results and reporting to EPA.
The photo gallery below and the inventory list that follows will best tell the story of this extraordinary effort.
Pipe Plant Before Rigging and Demolition of Operation
Machinery Rigging and Moving in Progress
Equipment Relocation Complete
Actual Inventory of Machinery Moved
Decommission, disassembly, removal, packaging, and loading was performed for the following production lines:
1. Coil Receiving and Storage
2. Track Welding Spiral Pipe Mill
- Coil Loading Carriage
- Auxiliary Drive Unit
- Flattening Device
- Moveable Strip Clamping Unit
- Cross Seam Welding Unit
- Ultrasonic Testing Machine
- Edge Milling Machine
- Horizontal Strip Guiding
- Main Drive Unit
- Vertical Strip Guiding Units
- Edge Pre Bending Device
- Forming unit
- Tack Welding Unit
- Pipe Cutting Unit
- Pipe Inspection Stands
- Pipe Inside Cleaning Machine
- TAB Plate Welding Stand
3. Hydrostatic Testing Machine
- Remove East Side Equipment
- Remove Pumps and Piping
- Removal of top truss
- Remove top frame sections Appx. 20 tons each
- Remove End Columns
- Remove Pipe Support Carriages
- Remove Bottom Frame Sections. Appx. 20 tons each
4. Epoxy Spray Coating
- Inbound Diablo Conveyor
- Inbound Conveyor #2
- Preheating Furnace
- External Shot Blaster
- Outbound Conveyor
- Intermediate Racks
- Diablo Inspection Device
- 1st Feed Roll
- 2nd Feed Roll
- Phosphating Device
- High-Pressure Washer
- Induction Heater
- Epoxy Spray Booth
- Air and water cooling devices
- 3rd Feed Roll
- Holiday Detector
- Outbound Conveyor
- Racks and Repair Stacker
- Diabolo Repair Conveyor
- Cooling Tower
- Marking Machine
- Air Compressor System
3. Crossover, Platform and Stairway Installation
Rig and Installation Rooftop Safety Equipment
This rigging and installation project required the gentle placement of large, awkwardly shaped steel structures onto the rooftop of a commercial building.
Prior to installation, all stairways and platforms were pre-assembled, rigged for transport, and deposited at the client’s facility.
Challenge: As can be seen in the photos below, the pre-fabricated pieces handled during this project required special care in order to maintain the integrity of the structures during the lift. Selecting proper pick points were a crucial aspect to the team’s success.
The type of structures and sizes included platforms, stairs, and landings ranging from 7’ to 38’ in length, 6’ in height, with an approximate width of 36”.
20+ total pieces were lifted and installed during two consecutive Saturday/Sunday shifts.
The crane operator had zero visibility to the landing location. The Lift Supervisor worked closely by radio with the Crane Operator and Crane Signaler to place the safety equipment on the roof, aided by the rigging team using tag lines to make minuscule adjustments, directing the piece to its final location.
Once correctly positioned, the platforms were bolted to existing rooftop anchors.
20+ total pieces were lifted and installed during two consecutive Saturday/Sunday shifts.
4. Stack Repair at Manufacturing Facility
Equipment Rigging at the Center of Custom Fabrication Project
In this unusual project, the SilMan Millwright team demonstrates the nimbleness and value that their multi-skill training can provide: rigging and installation of large equipment from a single team in one day.
The rigging team made two trips to the client’s location. First to remove one of two slide gates which were used as a template to engineer and fabricate a replacement.
Working with their electrical counterparts, a short-term replacement was fabricated in the field to keep the plant operational.
When the newly minted replacements were completed, the team returned to install and commission the two new units.
As an interesting twist to this situation, the crane operator had no visibility into the landing area on the opposite side of the building. The crane team positioned the units with microscopic precision by radio communication with the rigging team at the installation location.
Each slide gate weighs in excess of 4,000 pounds.
You may review a video and case study for this reverse-engineering and fabrication project on our portfolio page.
Rigging and Relocation Safety
Go behind the scenes on a real-life rigging project with the SilMan Safety Team, as they create a “Safe-Lift” plan, job site hazard assessment. The article includes a downloadable “Safe Lift Plan” checklist.
From Installation to Demolition
Multi-Skilled Millwright Team Delivers Unique Value
To close this piece, we asked Rob Hernandez to offer his thoughts about SilMan’s rigging projects. Hernandez is a project manager for the Specialty Services Division and is responsible for coordinating the mechanical team.
“Our Millwright team is a multi-skilled unit that never fails to surprise me. Thanks to their broad base of mechanical expertise, they bring a wealth of insight to every project. This value-added contribution protects our client’s best interest, which ultimately means maximizing up-time.
When it comes to rigging projects, their experience and rigorous ongoing training are invaluable. Moreover, familiarity with the complexities of each type of equipment to be deconstructed, rigged, and picked supports all aspects of the operation, especially safety.
Above all, I can’t let this opportunity pass without acknowledging our rigging leadership for these jobs. Here are some of our talented expert riggers whose work is featured in this article:
Tyde Biggerstaff
Caleb Siewell
Scott Cully
Paul Newell
Matt Anger
Shane Benson
Nick Goulart
In the end, of course, this value accumulates to the client.
The projects featured in this article are a perfect example of why our customers keep coming back: a cost-effective, multi-skilled team in one phone call.”
About the Company
SilMan Industries (previously SilMan Construction) is based in San Leandro, Calif., with Engineering and Field Operations offices in Tupelo, Miss. The firm provides integrated turnkey solutions in the Industrial, Manufacturing, Distribution, and Public Works sectors.
Notably, in 2010 SilMan Industries was contracted to dismantle and remove the NUMMI assembly line in Fremont, Calif., transport the equipment, and reinstall the system in Blue Spring, Miss., establishing Toyota Motor Manufacturing Mississippi (TMMMS). This high-visibility project ignited the company’s meteoric growth, laying the foundation for SilMan’s national service area.
For more information, please visit www.silmanindustries.com/about.